Marsden Bungalow Radical Retrofit: Joining the Two Storeys Together
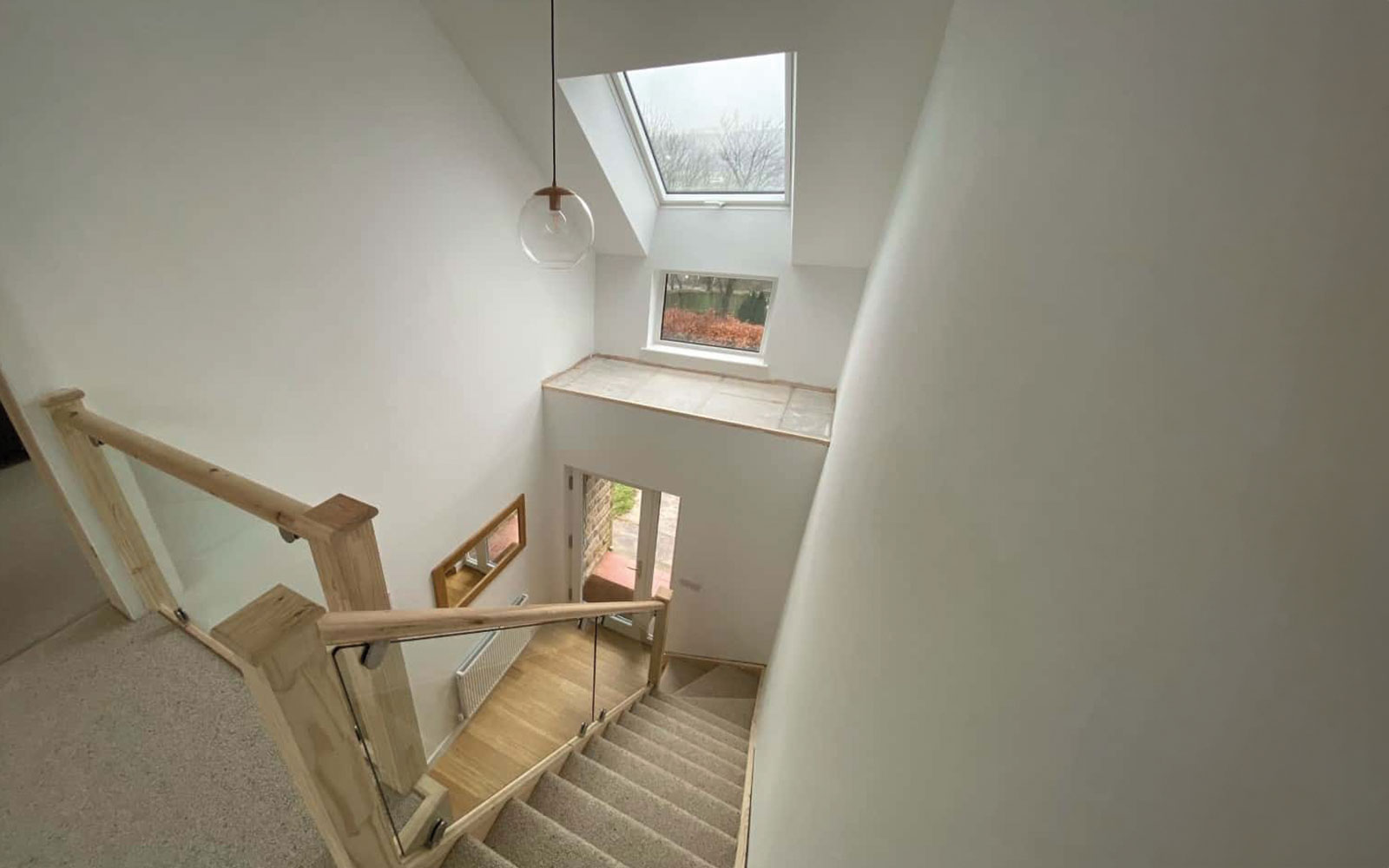
Following on from our previous blog on our hybrid masonry/ timber frame bungalow retrofit project we look at the crucial junction between the two storeys. To join the masonry cavity wall ground floor with the timber frame upper storey required a lot of careful detailing.
A key structural element of the build was a laminated timber ring beam going around all 4 sides of the building, transferring the weight of the new structure to the existing timber wall plate on the inner leaf of the blockwork wall This serves a structural role as it spreads the weight of the new structure consistently around the building. It goes across the top of window openings below without having to alter the lintels etc. Four steel joists are then hung over the timber ring beam (across the width of the house) and floor joists lain at right angles along the length of the house between them.
Continuity of airtightness and insulation
Where the timber frame meets the masonry wall, we have had to do careful detailing to ensure continuity of insulation and airtightness. For example, the airtightness layer in the upper floor has to come outside the timber ring beam and then join up with the parged masonry walls below.
The timber frame first storey utilises Intello Plus membrane as its airtightness layer. To join this up with the airtightness layer of the ground floor requires the crucial airtightness red line moving outside the ring beam to join up with the airtightness layer below. Because taking the airtightness layer to the outside of the ring beam is on the colder side of the build-up (outside the thermal envelope) there is a danger of interstitial condensation on the outside of the ring beam. Therefore, we used the vapour open (and airtight) Solitex Plus membrane at this junction on the outside of the ring beam to minimize the risk of interstitial condensation.
To help with continuity of insulation 60mm wood fibreboard is used around this junction. The timber frame roof, walls and laminated timber ringbeam were wrapped with the wood fibreboard to reduce thermal bridging.
Aims
The aim of the project is to use all of our knowledge and expertise gained from Passivhaus and EnerPHit projects to give our clients the most energy efficient solution within the constraints of their budget and the limitations of the existing building. We could not for example do much to the existing ground floor slab due to the levels and existing sound oak floating floor beyond the 25 mm PU insulation already in place which we are extending to all areas. So we have not intended to hit a particular standard – AECB or EnerPHit – but are simply taking a pragmatic approach based on our knowledge and experience.
We know we are able to optimize the airtightness because of our team’s expertise, but there are limits to this because we cannot affect the ground floor. We have not therefore made any commitment on airtightness levels with our clients.
Airtightness test
In spite of all this caution, the building team was ‘blown away’ by the first fix airtightness results of 0.9 ach @ 50 Pa. A big thank you to Alex Honey (then at Enhabit and now a Technical Director at our sister company QODA Consulting) who undertook the air testing for us. Another massive well done to our building team (Jude, Andy, Danny, Stevie, Isaac and George) who have excelled themselves yet again.
Bill Butcher, 21 Degrees