Cumberworth Radical Retrofit for Hard to Heat House
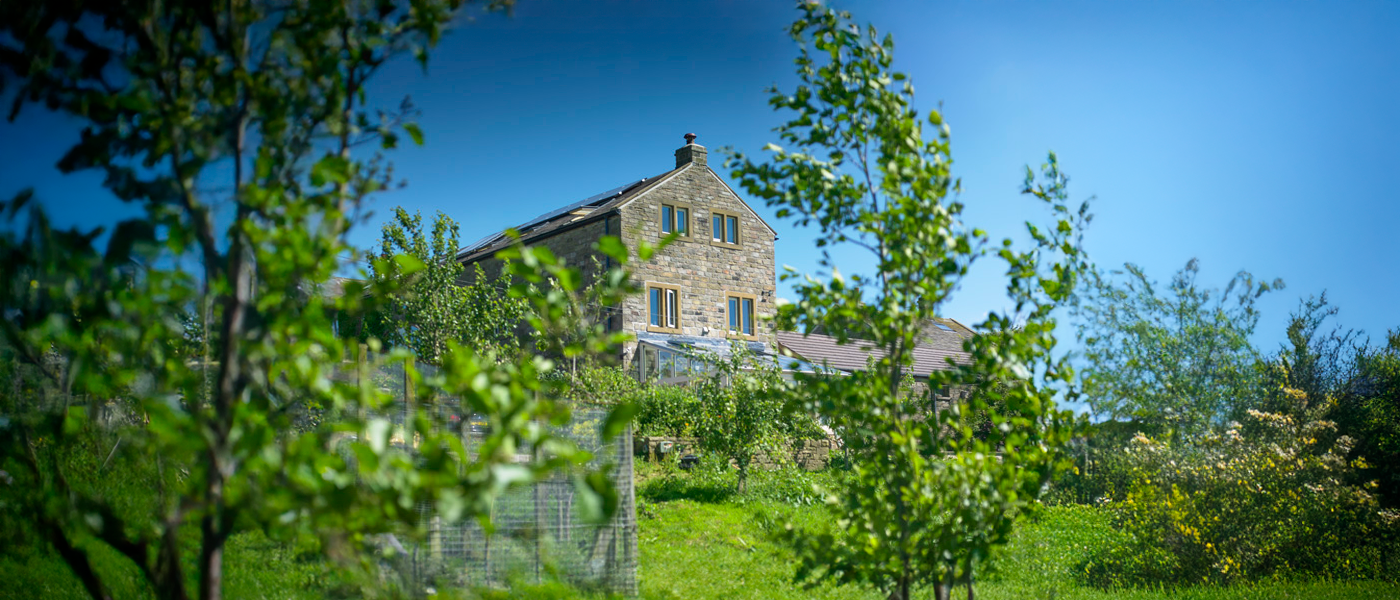
Green Building Company was contacted by private clients in 2013 to help improve the comfort levels and reduce the heating bills at a cold and hard to heat home in Cumberworth, West Yorkshire. We are proposing a ‘fabric first’ whole house retrofit strategy, based on Passivhaus principles and designed using PHPP (Passive House Planning Package), that could reduce the heating need of the house by an estimated 86%*. The project started on site in September 2014.
The fabric first approach will involve insulating walls, roof and floor, minimising thermal bridging, installing good airtightness, minimising thermal bypass with good wind tightness, and using a well designed heat recovery ventilation system. Heating will be provided by a ground source heat pump (the property has an adjoining boggy field), solar panels for domestic hot water, LPG for cooking, and a wood burning stove with back boiler for insurance against mains electric black outs (not too infrequent in this very exposed location). Photovoltaic PV solar panels will also be installed.
* Subject to continuous heating – see section below.
Hard to Heat
The house is situated in a very windy and exposed area, demonstrated by the numerous wind turbines nearby! The house is off mains natural gas and so the clients have been using LPG to heat the house and for domestic hot water. There is currently also a solid fuel fire in the living room, which is used a lot. However, the clients are finding it impossible to heat the house comfortably and it has been expensive and difficult to heat to a comfortable temperature because of the lack of insulation and many draughts. We undertook an airtightness test before we began the retrofit work to get an indication of how bad it is and the result was 16.9 m3/m2 hr @ 50 Pascals.
At the moment, our modelling in PHPP is suggesting that, once improved, the heating need will be in the region of 65 kWh/m2/ year. It is pretty immeasurable for something this draughty, but we think that to maintain a heat of 20 degrees in the winter, with the house in its present state, heating need would be in the region of 497 kWh/m2/year. Of course our clients didn’t actually heat it to that level, instead being cold and uncomfortable in the winter months. The peak heating load of the proposed renovated home would be 4KW at minus 10 degrees outside.
Hard to Treat
For aesthetic and planning reasons, the outside Yorkshire stone of the home needs to be preserved, so the project will require an internal insulation strategy. Concerns regarding interstitial condensation mean that we will need to be careful in the amount of internal insulation we can apply to walls. As a semi-detached property, we can’t raise the level of the roof. We’ve therefore got a restricted head height inside, which limits the amount of insulation we can put in the roof.
Stressed out
The project is particularly challenging as it is subject to a number of moisture ‘stresses’:
• Rain ingress from exposed west walls
• Potential for rising damp from groundwater
• Concerns about interstitial condensation from internal insulation
The moisture risk factor is different for the different wall structure types within the building.
A house of two halves
The 4-bed semi-detached house combines a 1990s conversion of a Victorian barn with a three storey 1990s extension, so our radical retrofit will require two different insulation strategies.
A) 1990s Extension
The 1990s extension has cavity wall construction with a polystyrene ‘poly-back’ insulation block in the cavity. One of the problems is that the insulation is only 30mm thick and is not continuous – the mortar joints create numerous repeating thermal bridges.
Strategy
We have decided not to add further insulation to the cavity itself for a number of reasons. The cavity is likely to be very uneven because of the uneven nature of the back of the reclaimed stone used on the outer leaf and so would be inconsistent. As is typical, the cavity will also have mortar droppings which would also prevent a consistent cavity fill. Insulating the cavity might create problems by preventing ventilation of the cavity and so worsening rain penetration . The site has very high rain exposure, which could impact on the effectiveness of the cavity insulation.
IWI strategy:
We still haven’t completely finalised the strategy but it is looking like we will use mineral wool batts held in place with studs made of extruded polystyrene (XPS polystyrene) and OSB board, with an intelligent membrane to allow any moisture in the wall to be released.
We also haven’t decided whether we should we remove all gypsum plaster in the extension (it is a wet plaster system and has been well done). From an airtightness point of view the walls are not so bad (though the junctions between the floors and the walls aren’t great). We’re not sure whether we should hack off all the plaster and then parge with cement and sand/ lime.
B) Barn Conversion
The late 19th century barn was converted in the 1990s to meet the then building regulations but where, unfortunately, there was no consideration for airtightness. The barn walls are typical of construction of that era, with inner and outer stone facing filled with rubble and the occasional through stone. Unlike the extension, the barn does not have a damp proof course and so is at risk from rising damp.
IWI strategy:
In terms of IWI options, we were initially thinking of adding vapour open wood fibre insulation to the internal walls but are currently considering an exciting new capillary open mineral insulation board not currently available in the UK which has some excellent breathable properties. We would probably then follow this with breathable lime plaster.
We are proposing to remove the 1990s dot and dab plasterboard and strip the walls back to the stone. We would need to parge coat the walls with sand/lime and cement for wind and airtightness reasons. There is a current debate whether we remove the existing parge coating water repellent layer on the barn walls. Jude our site foreman and the team are understandably quite reluctant to undertake this!
Your feedback on our approach would be very welcome – we’d be especially interested to hear your thoughts on the internal insulation choices and interstitial condensation issues. We’ll be blogging regularly throughout the project, sharing the junction detailing etc.
Bill Butcher, Founding Director