Transforming tin barns into an EnerPHit-certified home
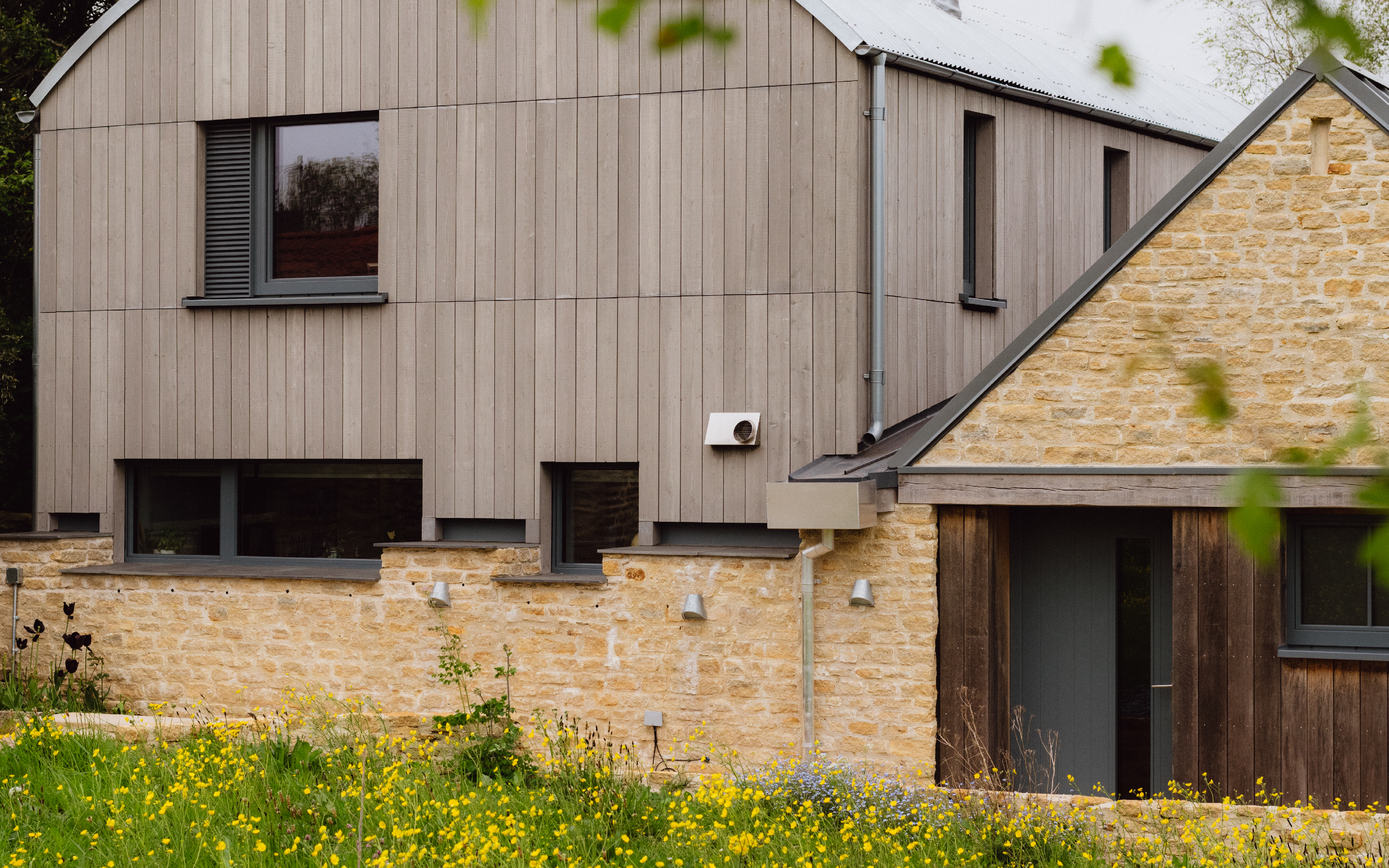
Located in the serene Marshfield Conservation Area near Bath, the Tin Barn EnerPHit project demonstrates the potential of sustainable architecture. The project aimed to convert Grade II listed derelict agricultural barns into a modern, energy-efficient home, achieving the exemplary Passivhaus retrofit standard: EnerPHit certification.
The challenge
Our clients sought to transform the derelict barns into a Passivhaus home that’s manageable in scale and cost-effective to operate. Their vision included a sustainable living space, a workspace, and a vegetable plot merging with the wildflower meadows and countryside beyond.
The energy-efficiency goal was to create a high-performing home that minimises environmental impact, meeting the stringent requirements of Passivhaus certification. The initial state of the buildings posed a significant challenge, with the barns in a severe state of disrepair, one reduced to a ruin with only rudimentary wall structures standing.
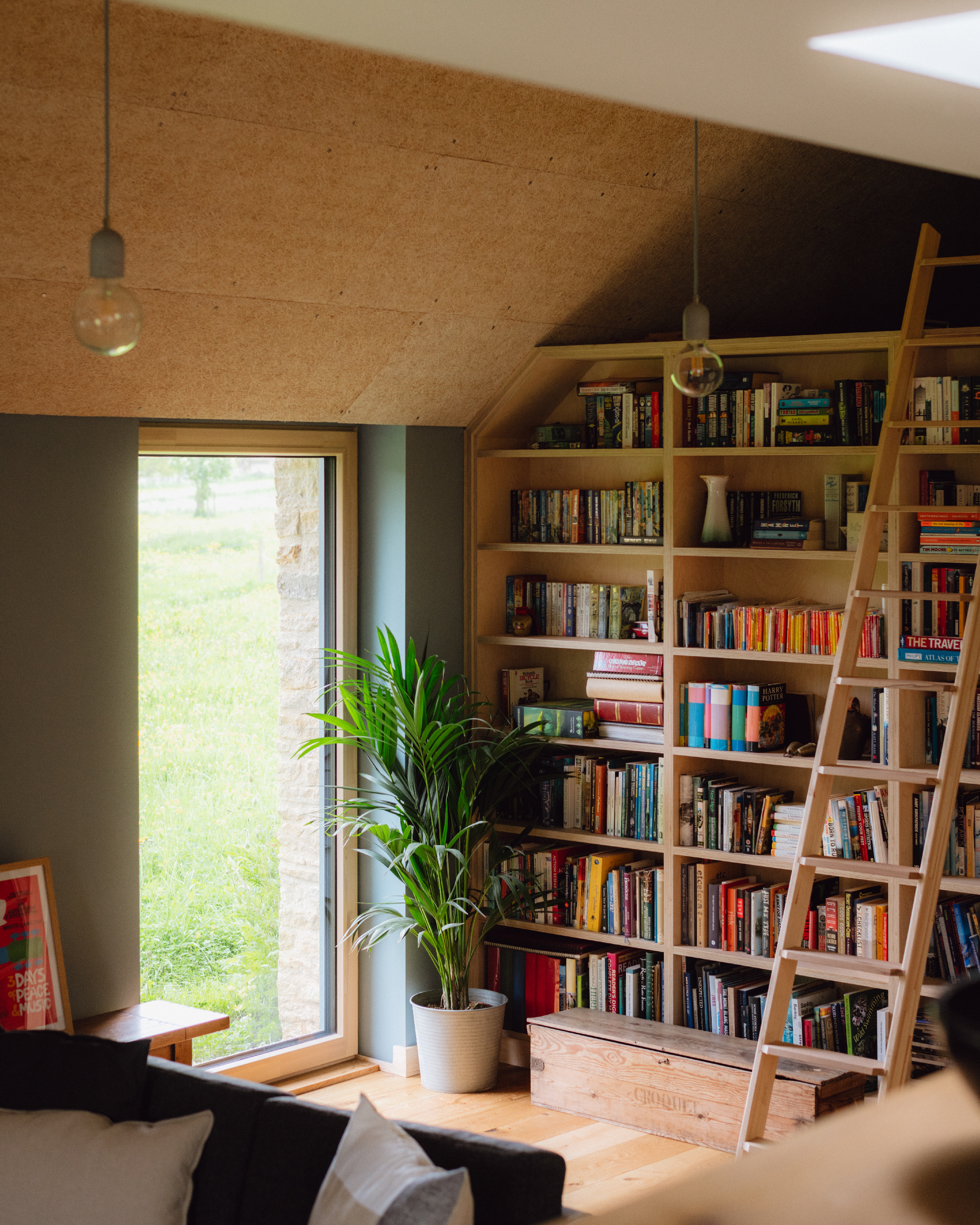
Our solution
Having used 21° products in previous projects, Arbor Architects proposed that our solutions be used for this particular project, too.
To provide fresh, filtered air into the property while retaining most of the energy used to heat it, we recommended a mechanical ventilation with heat recovery (MVHR) system – more specifically, Ubiflux Vigor units. These were integrated with a rigid, galvanised route and branch ventilation system within the floor build-up for two barns. We worked in close collaboration with Arbor to overcome design constraints posed by vaulted ceilings.
For the perfect blend of aesthetic appeal and energy efficiency, we also supplied a GBS98 timber entrance door, alu-cladGBS98-A triple-glazed windows, and lift-and-slide doors. We were able to supply products colour matched in different materials. These were specified with RAL-7031 (Blue Grey) on the exterior, and finished with Nature Effect clear stain on the interior.
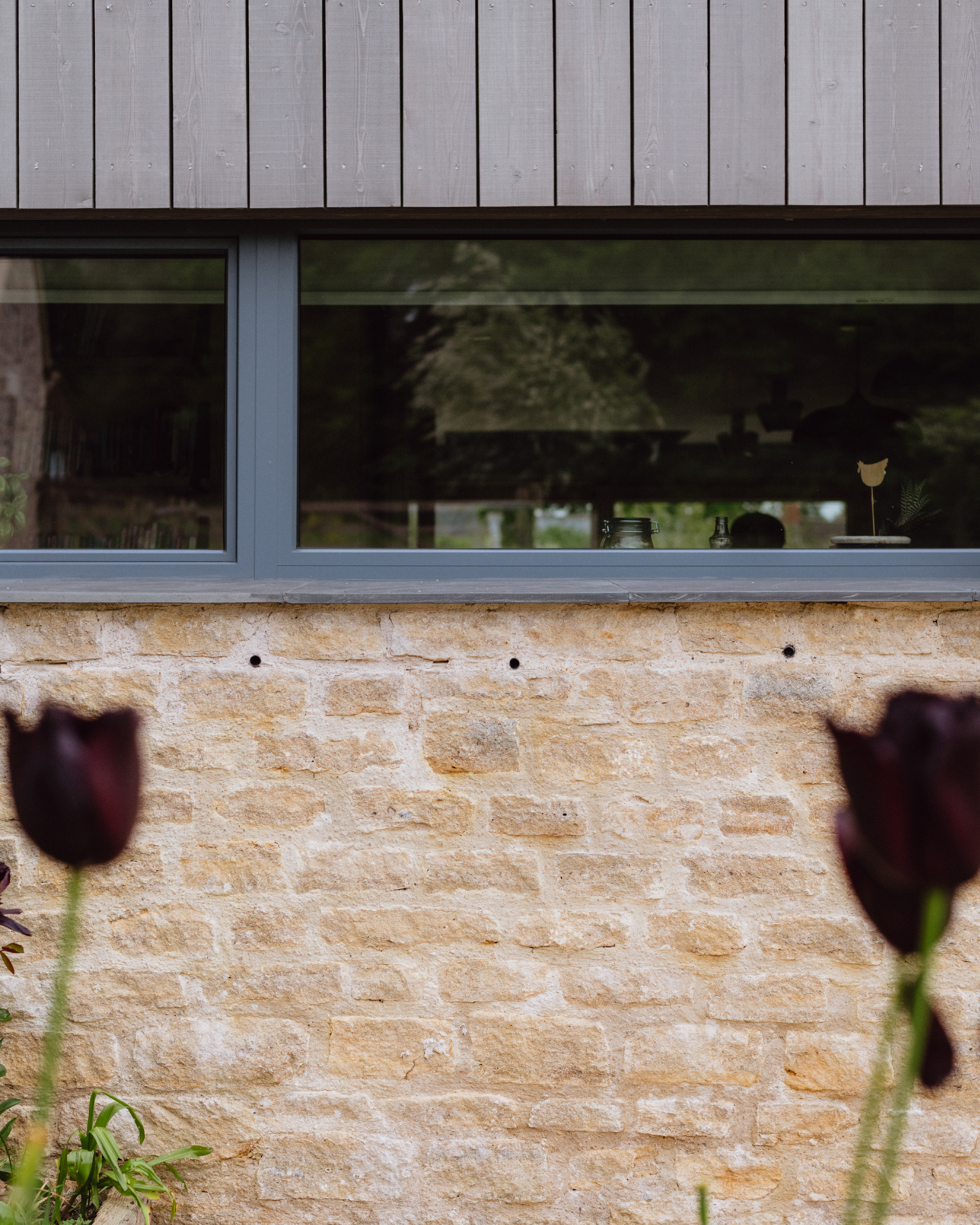
The outcome
The building's embodied carbon is impressively low at 347 kg CO2e/m2 GIA, nearly half the RIBA 2030 target of 600 kg CO2e/m2 GIA. The fabric makeup utilises an entirely timber build-up with Propassiv airtightness boards and 350mm TGI joist filled with Warmcel cellulose insulation. Achieving EnerPHit certification highlights the project's commitment to high performance and longevity, significantly enhancing operational efficiency and reducing long-term energy consumption.
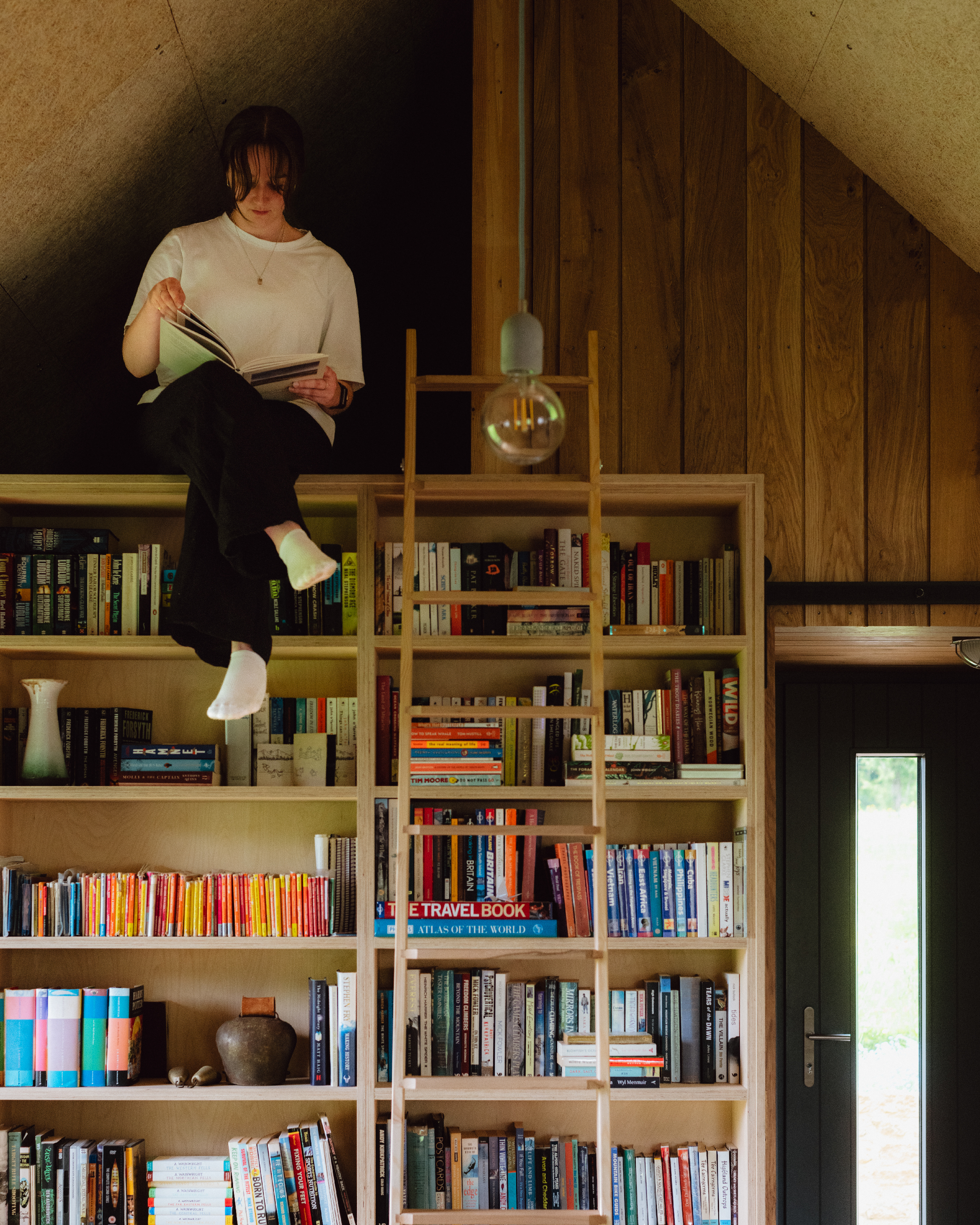
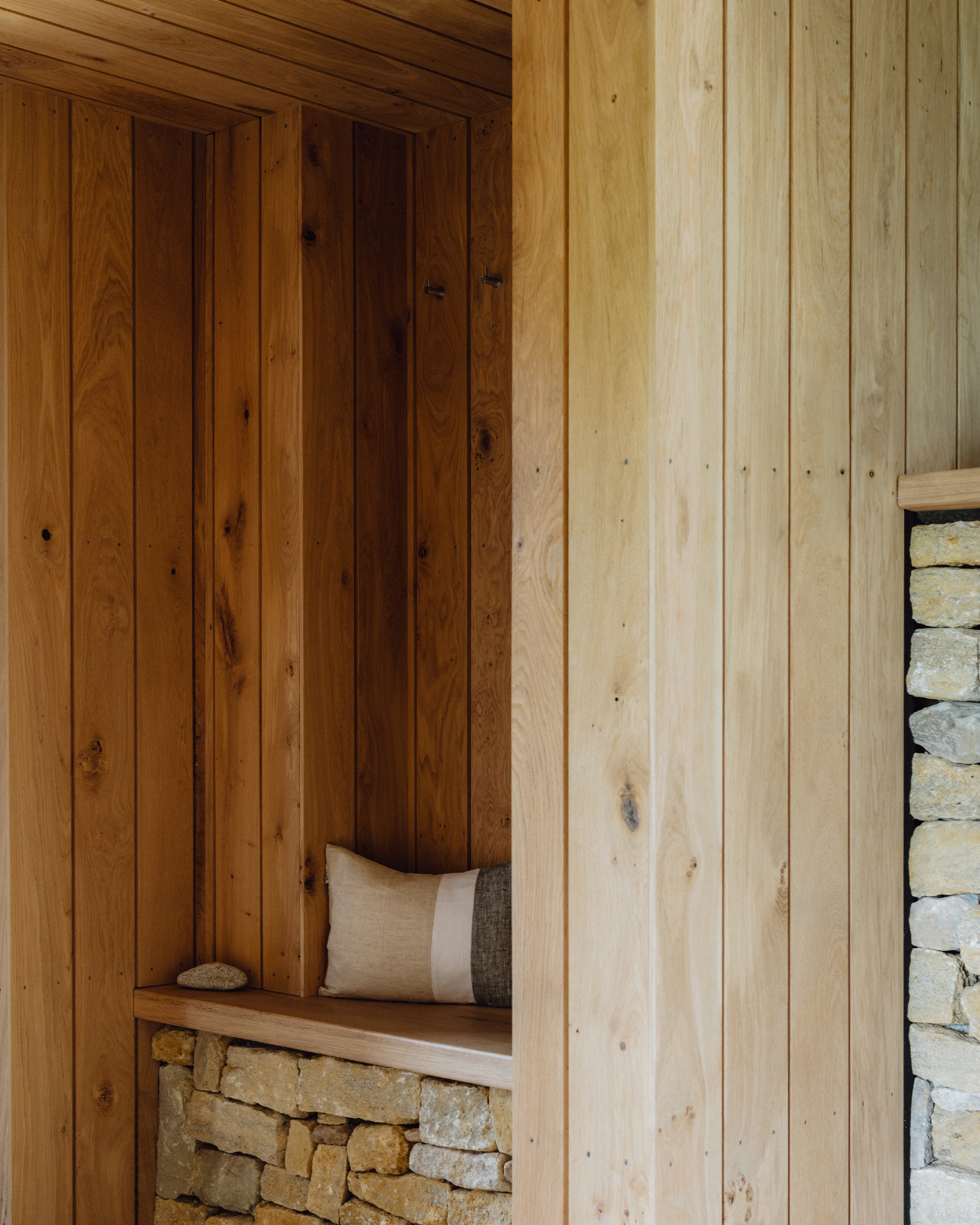
The architectural design incorporates materials such as corrugated metal roofing, sandstone walls, and larch cladding, blending with the rural surroundings. Internally, the richness and textures of oak panelling, stone walls, and exposed ceilings enhance the building's character. This design is beautifully complemented by the doors and windows supplied by 21°, which have received praise from the clients for their elegant finish, efficiency, and effectiveness – particularly during storms when their noise-insulating properties were truly put to the test. Finally, the different opening options provide flexibility for ventilation on warmer days, seamlessly blending the indoors and outdoors.
Homeowner & client
The Tin Barn project is a standout example of where architectural excellence, innovation, and sustainability intersect. What were once derelict agricultural buildings are now a bright, airy, and calming living environment that meets stringent energy-efficiency standards, all while promoting superior health and comfort.
To discover how we can help with your energy-efficient home project, get in touch.