Greendale Cottage
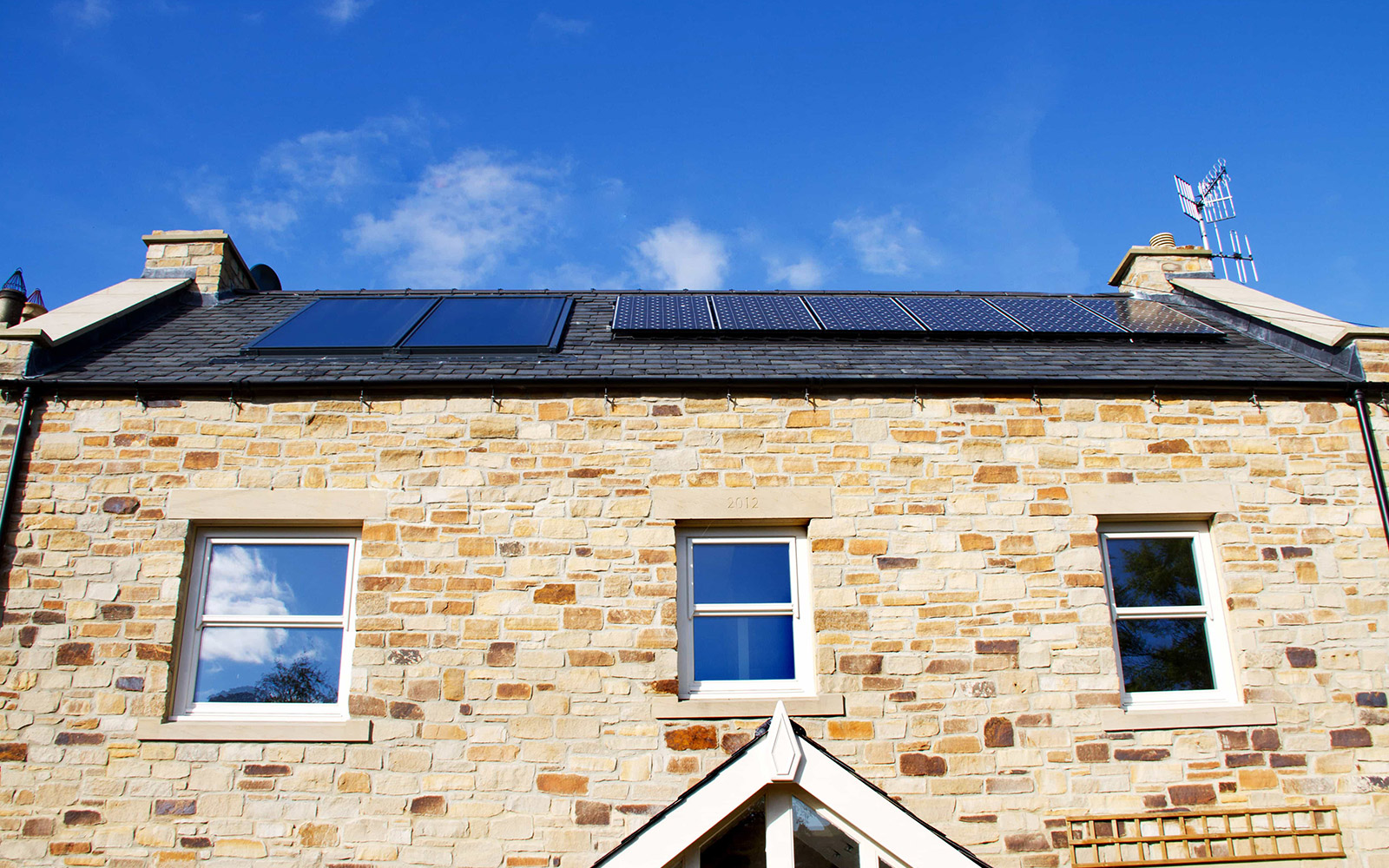
Phil & Joy Newbold undertook a self-build detached 3-bed Dales cottage using Passivhaus principles, in Upper Weardale, County Durham an Area of Outstanding Natural Beauty (AONB). As Phil is an architectural technician & Certified Passivhaus Consultant he undertook the project and site management and designed the house using Passivhaus principles and with the aid of Passive House Planning Package software. 21°’s PERFORMANCE windows, MVHR systems and airtightness products were specified for the project.
Planning issues in AONB
The project has faced a number of challenges, not least the planning requirements for a Conservation Area and a designated Area of Outstanding Natural Beauty. The Newbolds’ desire for a certified Passivhaus was scuppered by the planning department’s insistence that they retained the L-shaped floor plan of the original planning consent as well as insisting upon the house meeting local vernacular aesthetic requirements including random stone walls, natural slate roof and sliding sash windows. Despite not achieving Passivhaus certification criteria, the resulting home still achieves an impressive thermal performance with building fabric U-values of approx 0.1, an airtightness result of 0.59 @ 50 Pa and a predicted space heating requirement of around 18 kWh/m2/K.
Airtightness & woodburning stove
An unusual aspect of the project has been the use of a 10Kw Woodfire F12 room-sealed woodburning boiler stove. This is the home’s sole heating source and has a back boiler that provides up to 8.5Kw of hot water in the winter and also heats towel rails in the bathrooms plus a heat-leak radiator in the linen cupboard. Integrating the stove and masonry chimney stack within the timber frame structure was a challenge in itself. Airtightness detailing around the stove was achieved through using grommets around pipes with taped Pro Clima Intello membrane around any breaks through the timber frame. So, unusually for a Passivhaus-inspired project, the cottage has two chimneys stacks – one a false one for the MVHR air inlet and one for the twinwall stainless steel stove flue
Mock sliding sash triple glazed timber windows
21 Degrees supplied its triple glazed mock sliding sash windows and external doors for the project at a whole window U value of 0.91 W/m2K. The planning department had to inspect a sample of the window before approval and they were satisfied that it was a good facsimile of a sliding sash window.
Phil Newbold - Client
MVHR heat recovery ventilation
21° also designed, supplied and commissioned the PAUL Novus 300 MVHR system for the project. Phil installed the rigid steel ducting as well as the MVHR unit himself.
Phil Newbold - Client
Airtightness measures
21° also supplied Pro Clima airtightness products such as Intello Plus membrane, cable and pipe grommets and Tescon tape.
Project details
Architect
Awards
The project won the the National Award for “Best New Home” at the 2014 LABC Building Excellence Awards.
Completed
2013