Connect Housing Boggart Hill project, Leeds
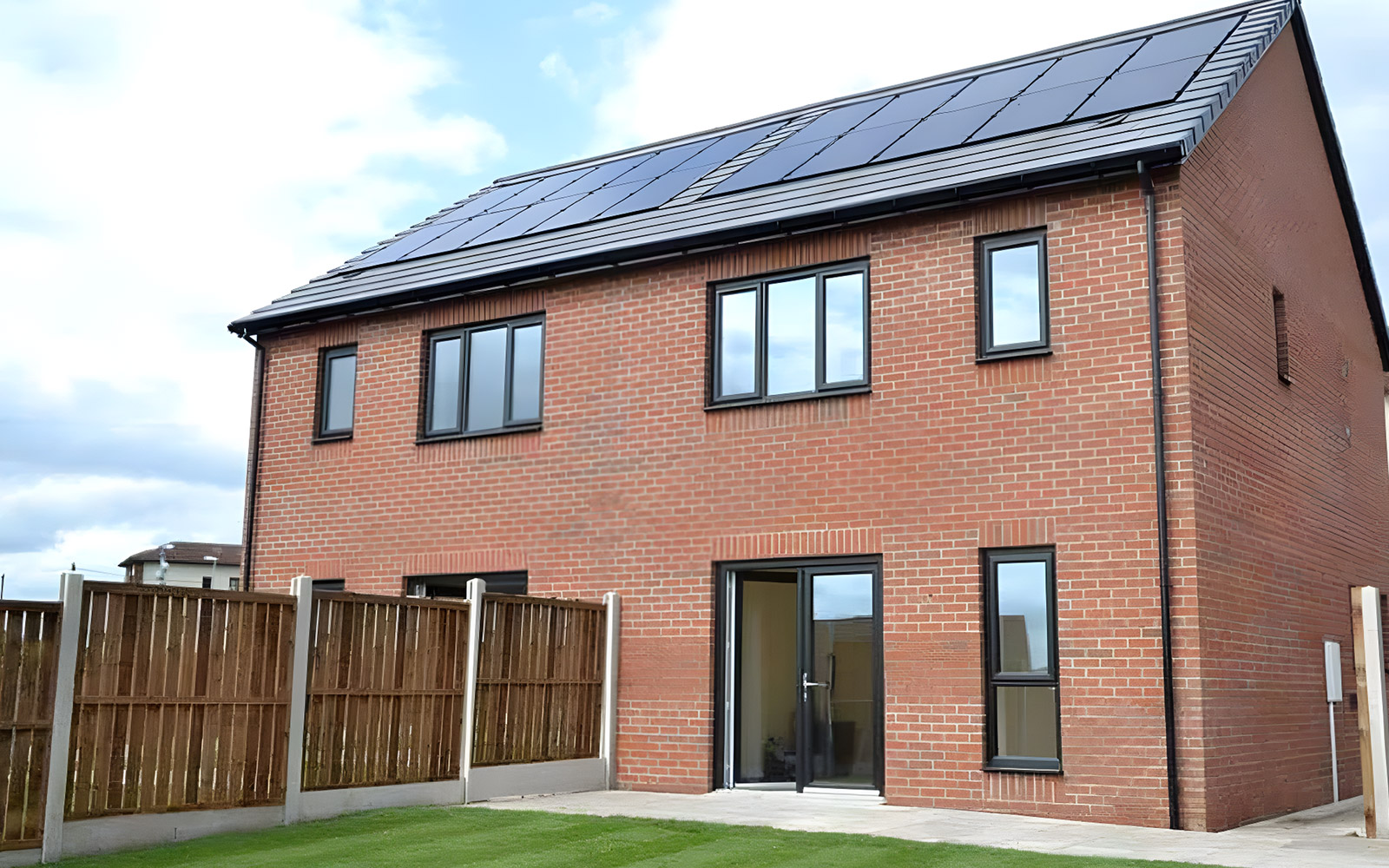
Social housing project achieves certified Low Energy Building Standard.
Connect Housing has recently completed a development comprising 10 semi-detached 2 bedroom homes, certified to the Passivhaus Institut’s Low Energy Building Standard (LEBS). The homes are located on Boggart Hill Road in north Seacroft, close to Roundhay Park, Leeds. The project was the first Connect Housing had undertaken using Passivhaus design principles and went down the LEBS route for certification as orientation issues meant that the project would not be able to meet the full Passivhaus standard. To achieve the LEBS requirements the project had to achieve an air pressure rating of less than 1m3/h.m2. The homes were built using timber frame off-site construction.
21 Degrees designed, supplied and commissioned the MVHR system for the project, with the PAUL Focus 200 MVHR unit and rigid steel spiral wound ducting.
Key features
- External Wall U-value 0.13 W/m2K (Timber frame. 100mm brick, 50mm cavity, 120mm Xtratherm XT-TF, 9mm OSB, 50mm Xtratherm XT-TF)
- Roof U-value 0.16 W/m2K (25mm Xtratherm XT-PK, 100mm Xtratherm XT-PK)
- Ground Floor U-value 0.13 W/m2K
- Triple glazing U-value 0.8 W/m2K
- External Doors U-value 1.0 W/m2K
- Thermal bridging to enhanced accredited details
- MVHR (Paul Focus 200)
- Electric panel heating (no gas) – primary and secondary hearing circuits
- Solar PV 3 KW array with battery storage (Ephase 1.2kWh)
- 100% LED lighting. Dimplex EC-Eau 150L Hot Water Cylinder
Monitoring
Residents moved into the homes in November 2017 and Connect Housing are undertaking ongoing monitoring energy bills, solar electricity production, humidity and temperatures within each of the homes.
MVHR mechanical ventilation with heat recovery
21 Degrees designed, supplied and commissioned the MVHR system for the project, incorporating the PAUL Focus 200 MVHR unit and rigid steel spiral wound ducting. An A-rated re-circulating cooker hood provides primary grease filtration while the kitchen extract filter prevents grease from entering the ducting system. There is a boost switch in the Kitchen allowing occupants to boost the system when a higher extract rate is required. Due to space constraints the MVHR units were housed within a cupboard in the Master bedroom, not somewhere 21 Degrees usually locates them, so ensuring quiet sound levels from the MVHR system and unit was especially important.
As the homes gain free electricity from solar PV panels on the roof, the owners are assured that MVHR system is effectively free to run.
MVHR maintenance
Connect Housing’s in-house property services team undertake the routine MVHR filter replacement for the homes. 21 Degrees MVHR Design Manager Tom Heywood came over to deliver a handover toolbox talk to the team on how to maintain and adjust the MVHR system.
Phil Lacey, New Homes Project Manager at Connect Housing
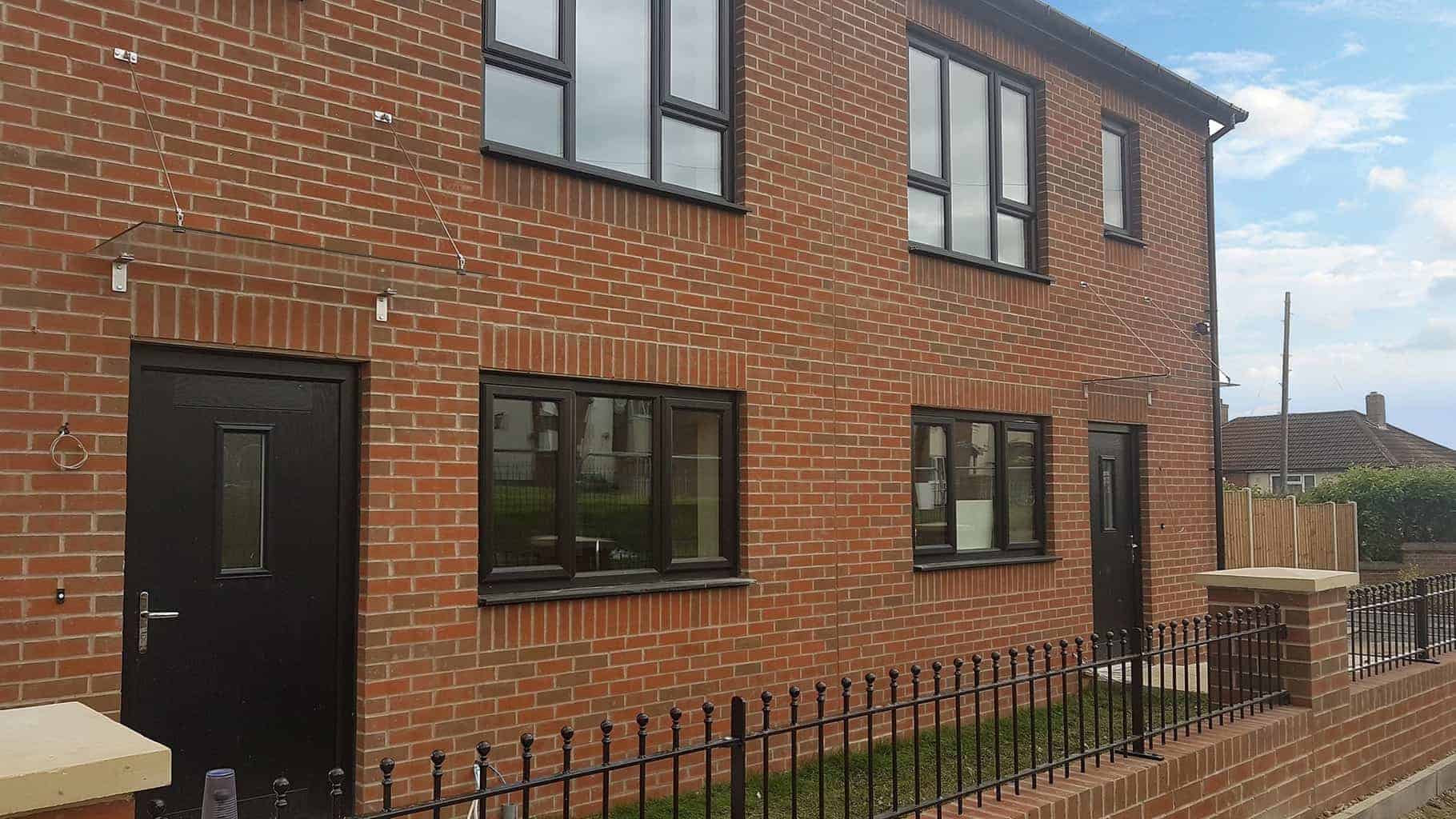
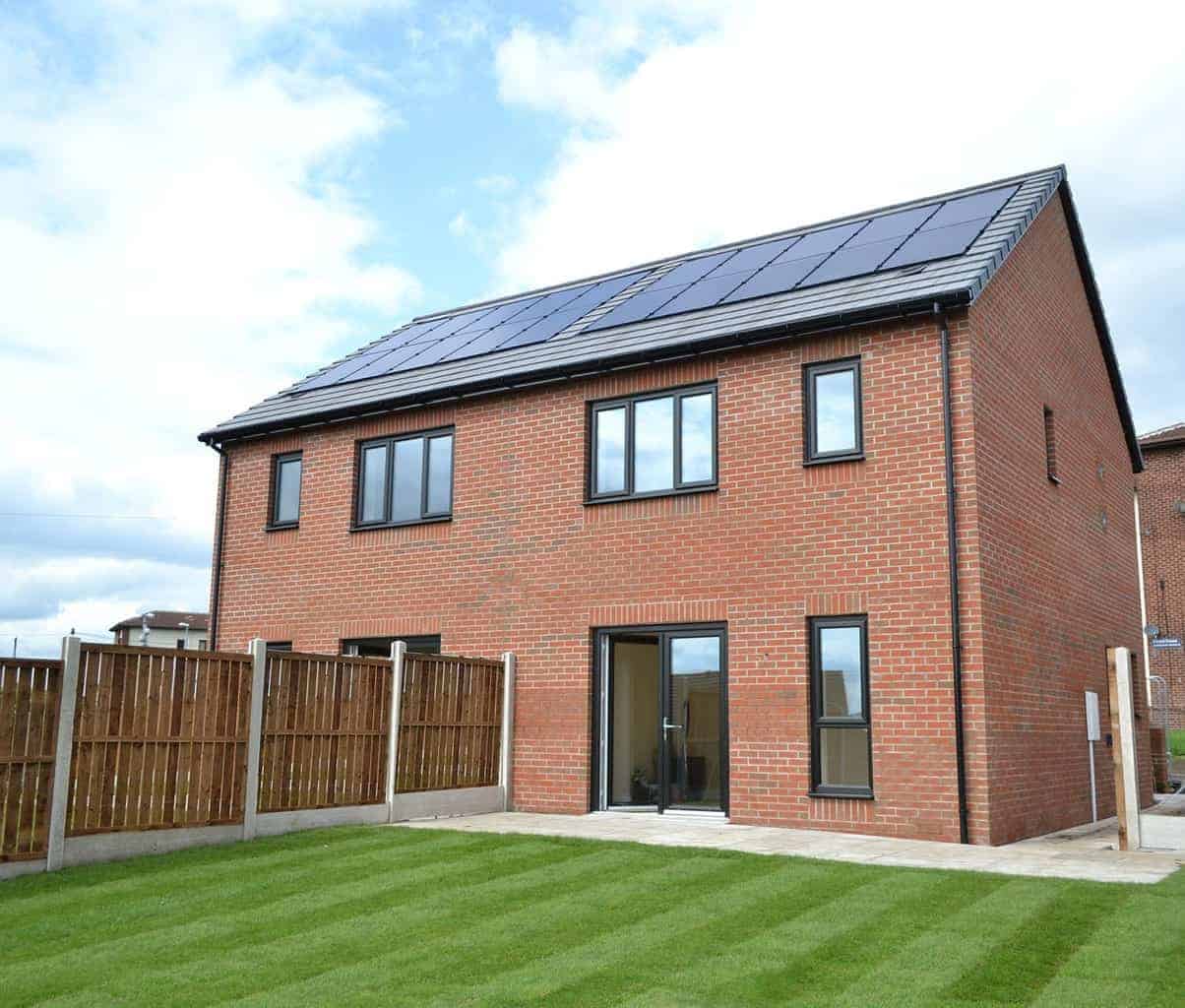